Jay Tu
Professor
- Phone: (919) 515-5670
- Email: jftu@ncsu.edu
- Office: Engineering Building III (EB3) 4164
- Website: http://mae.ncsu.edu/research/laser_lab
As an educator, Dr. Tu’s highest priority is to teach strong fundamentals and to relate them to real-world problems. At the graduate level, Dr. Tu teaches Principles of Structural Vibration (MAE 513). This course is an introductory course on mechanical vibration that follows a traditional exposition. He places a strong emphasis on the formulation of vibration problems and an additional emphasis on its broad applicability beyond mechanical systems, such as music and science. Dr. Tu will introduce a new course in Precision Laser Material Processing in the coming semesters for both graduate students and seniors.
At the undergraduate level, Dr. Tu teaches Manufacturing Processes (MAE 496M) and Analysis for Mechanical Engineering Design (MAE 415). In MAE 496M, the goal is to review the major manufacturing processes, how design is carried out using these processes, and how these manufacturing processes solve engineering problems. Dr. Tu shows through proper dimensioning how different processes are integrated to achieve required tolerances. In MAE 415, Dr. Tu teaches design from the perspective of how required precision is achievable; bringing manufacturing into the design process from the beginning.
The role of lasers in engineering is fascinating; lasers are unique in that they operate on the basis of a purely human-made physical phenomenon and their use brings in understanding of electrodynamics, mechanics, and thermodynamics, making the subject rich and complex — the number and variety of applications are almost limitless. Dr. Tu expects his graduate students to have a strong sense of urgency and be an active thinker to attack problems, moving forward aggressively. This philosophy will help students to develop into confident solvers of engineering problems, making them well-prepared for the workplace.
Outside of work, Dr. Tu enjoys spending time with his family and playing tennis. As hobbies, he enjoys photography, collecting classical cameras from the perspective of precision machine design, and rebuilding musical instruments based on engineering vibration analysis.
Publications
- A novel auto-gaping magnetic pole system for inner surface finishing of non-circular pipes using magnetic abrasive finishing process
- Heng, L., Tu, J. F., Im, H., Kim, H.-J., Chanchamnan, S., Kim, J. S., & Mun, S. D. (2023), JOURNAL OF MAGNETISM AND MAGNETIC MATERIALS, 580. https://doi.org/10.1016/j.jmmm.2023.170909
- Digital Synthesis of Realistically Clustered Carbon Nanotubes
- Susi, B. T., & Tu, J. F. (2022), C-JOURNAL OF CARBON RESEARCH, 8(3). https://doi.org/10.3390/c8030034
- Laser Spot Welding and Electric Contact Points Using Copper/Single-Walled Carbon Nanotube Nanocomposite Synthesized by Laser Surface Implanting
- Tu, J. F., Rajule, N., & Mun, S. D. (2021), JOURNAL OF COMPOSITES SCIENCE, 5(3). https://doi.org/10.3390/jcs5030087
- Fabrication of precision meso-scale diameter ZrO2 ceramic bars using new magnetic pole designs in ultra-precision magnetic abrasive finishing
- Heng, L., Kim, J. S., Tu, J.-F., & Mun, S. D. (2020), CERAMICS INTERNATIONAL, 46(11), 17335–17346. https://doi.org/10.1016/j.ceramint.2020.04.022
- Novel Characterizations of Mechanical Properties for a Copper/Single-Walled Carbon Nanotube Nanocomposite Synthesized by Laser Surface Implanting
- Tu, J. F., Rajule, N., & Mun, S. D. (2020), C-JOURNAL OF CARBON RESEARCH, 6(1). https://doi.org/10.3390/c6010010
- Difficult Engineering Concepts Better Explained
- Tu, J. F. (2020). , . https://doi.org/10.1142/11652
- Effect of the Magnetic Pole Arrangement on the Surface Roughness of STS 304 by Magnetic Abrasive Machining (vol 15, pg 1275, 2014)
- Yin, C., Tu, J.-F., Lee, J. H., Yang, G. E., & Mun, S. D. (2019, June), INTERNATIONAL JOURNAL OF PRECISION ENGINEERING AND MANUFACTURING, Vol. 20, pp. 1069–1069. https://doi.org/10.1007/s12541-019-00158-1
- Feasibility Study of Microneedle Fabrication from a thin Nitinol Wire Using a CW Single-Mode Fiber Laser
- Tu, J., & Reeves, N. (2019), OPEN ENGINEERING, 9(1), 167–177. https://doi.org/10.1515/eng-2019-0023
- Molecular dynamics simulations of the wetting behavior of carbon nanotubes in liquid copper
- Susi, B. T., & Tu, J. F. (2018), COMPUTERS & FLUIDS, 172, 19–28. https://doi.org/10.1016/j.compfluid.2018.06.004
- Laser synthesis of a copper-single-walled carbon nanotube nanocomposite via molecular-level mixing and non-equilibrium solidification
- Tu, J. F., Rajule, N., Molian, P., & Liu, Y. (2016), JOURNAL OF PHYSICS D-APPLIED PHYSICS, 49(49). https://doi.org/10.1088/0022-3727/49/49/495301
Grants
- EAGER Collaborative Research: Nanocomposite Copper Tooling for Faster Cycle and Improved Precision in Plastic Molding Proof of Concept
- SGER: Synergistic and Inherently Stable Laser/Plasma-Jet Welding Processes: Proof of Concept
- Quantitative Roundness Design and Quality Assurance for Ultra-Precision Assemblies with Significant Error-Scaling Problems
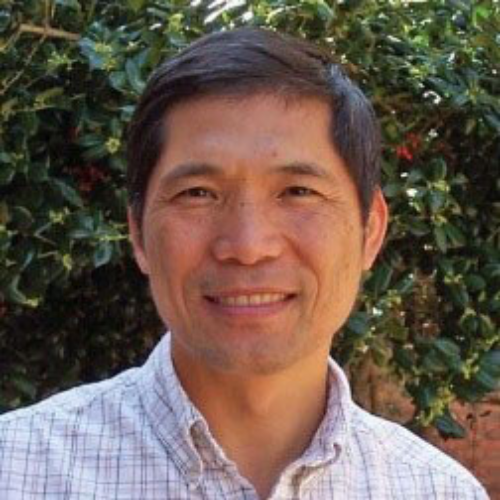